空心薄壁构件液压成型技术的研发和应用
文|徐勇, 张士宏
随着汽车、航空航天制造业对产品性能和轻量化要求的不断提升,采用空心结构替代传统的实心部件已成为重要发展趋势。管材液压成形技术作为主要的轻量化成形技术之一,适于成形具有复杂变截面的整体化空心构件,可以大量替代传统铸造和冲焊工艺,因而近年来得到广泛应用。但是,液压成形仍不能完全解决具有大变形量和小圆角特征结构的零件制造加工。为了进一步提高材料的成形性并避免起皱和破裂等缺陷的发生,中国科学院金属研究所塑性加工先进技术课题组结合液压成形与精密锻造的技术特点和优势,研发出了一种适用于空心薄壁构件的液压锻造新技术并开展了示范性应用。
材料和零件
本文以某奥氏体不锈钢Ω形零件成形为例,其具体结构尺寸如图1所示。零件的端部直径为φ128mm,中部直径达到φ175mm,其最大变形量将近40%,零件边缘位置的过渡圆角仅为1mm,壁厚为1.5mm。
液压锻造工艺原理
液压锻造工艺采用空心管件作为初始坯料,而不是传统锻造工艺中采用的实心固体材料。在这种工艺中,流动介质被注入空心管件中,同时应用可移动的冲头密封部件两端,并对液态介质加压,同时配合相应的轴向进给,将工件成形到指定形状。
液压锻造工艺原理如图2所示。整个成形过程主要分三个阶段:低压预胀形、中压锻造和高压整形。首先将液体注入管状坯料,然后应用两个冲头进行密封。通过液压成形工艺,将管坯加工到过渡形状,用外部增压器对内部液体进行增压,用以代替冲头运动,具体如图2(a)所示。当内部液体压力保持或者随着实际锻造力增加,将过渡形锻造到近终形状,如图2(b)所示。在锻造过程中,尽管没有必要轴向进给管材,但是因锻造过程引起了轴向长度减小,为了密封管材两个端部,必须给定冲头行程,并且该行程要等于锻造工具的行程。
最后,继续对内部液体进行增压,迫使管材充分填充模具型腔,尤其是边界位置,具体如图2(c)所示。冲头和锻造工具同时保持静止。当成形结束后,冲头和锻造模具返回初始位置,打开闭合模具。
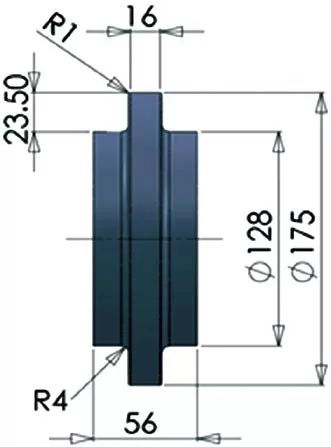
图1 目标零件的结构尺寸
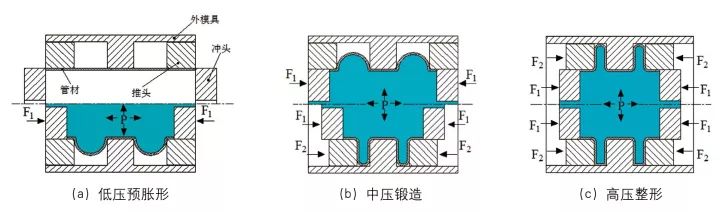
图2 空心薄壁构件液压锻造工艺原理
有限元模拟和实验验证
应用有限元模拟软件ETA.Dynaform 5.9.1进行数值模拟分析。图3给出模拟所采用的有限元模型,所用管坯长度为212mm,外径为φ128mm。模拟过程也分为三个阶段:低压胀形、中压锻造和高压整形。为了简化模型,只模拟工具与管材接触面。建立Belytschko-Tsay 5节点四边形壳体单元,管材单元的数目为3976。冲头、工具和外模具设置成三维分析的刚度单元,由于单元的类型缘故,刚度体不划分网格和分析。基于罚函数原理规定模具和管材之间的接触。应用库伦摩擦法则,将模拟中管材和模具表面的摩擦系数定义为0.1。
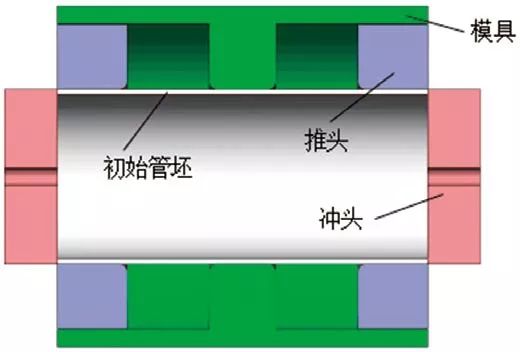
图3 有限元模拟模型
模拟和实验中所采用的三种载荷路径,也就是内部载荷和冲头行程之间的关系,如图4所示。三种载荷路径分别定义为路径1、2和3。三种载荷路径的不同主要集中在液压和锻造工步,而最后阶段的整形压力相同。
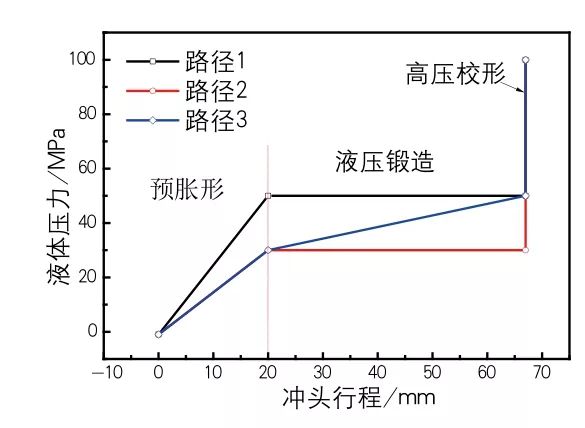
图4 数值模拟和实验中所采用的载荷路径
在路径1中,液压胀形力为50MPa,在后续的锻造阶段保持该数值。在路径2中,液压力为30MPa,在后续的锻造阶段保持不变。在路径3中,液压力在锻造阶段,由最初的30MPa增加到50MPa。冲头和锻造工具的行程对于所有的载荷路径都相同。除此之外,将管材自由胀形成“Ω形”,并将该形状作为液压阶段的过渡形。模拟和实验都围绕三种不同的载荷路径展开分析。
通过应用载荷路径1,如图5所示,锻造阶段,管材中间区域发生胀破。由于模具的设计为一模两件,所以在液压成形过程中每一部分只有一侧的轴向进给。所以当内部压力的增加速度大于冲头轴向进给的行程时,不能够提供足够的材料用以周向扩展,而导致液压过渡形的严重减薄。
图6给出了采用载荷路径1的变形工件的壁厚分布,管材在液压胀形阶段为自由胀形。某种程度上讲,最大的变形位于变形区的中部,最小壁厚已经减小到1.08mm,液压胀形后的减薄率为28%。因此在随后的锻造阶段,将管材成形到近终形状时,容易在过度减薄区域产生胀破。
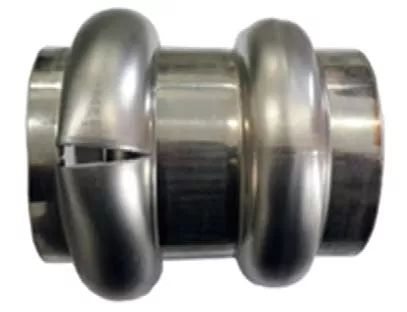
图5 锻造阶段管材中间部位胀破

图6 采用载荷路径1的变形工件的壁厚分布
如图7所示给出了载荷路径2的模拟结果。从图中可以发现,液压阶段当内部液压力保持在30MPa时,能够避免壁厚过度减薄。图7(a)给出成形部件的厚度分布图,厚度减薄率在15%以下。然而,由于后续的锻造阶段管材内部的液压力相对较低而引起的塑性不稳定,致使锻造工具压缩管材到过渡形时出现折叠和褶皱缺陷。从图7(b)看出,锻造阶段折叠较为严重。情况最严重时,即使后续整形压力非常高也无法消除褶皱,如图7(c)所示。图8所示为应用载荷路径2所做实验中的折叠。
根据路径1、2得到的模拟和实验结果,本研究设定了加载路径3。图9显示采用载荷路径3成形的工件没有裂纹和折叠,数值模拟和实验均体现出该趋势。
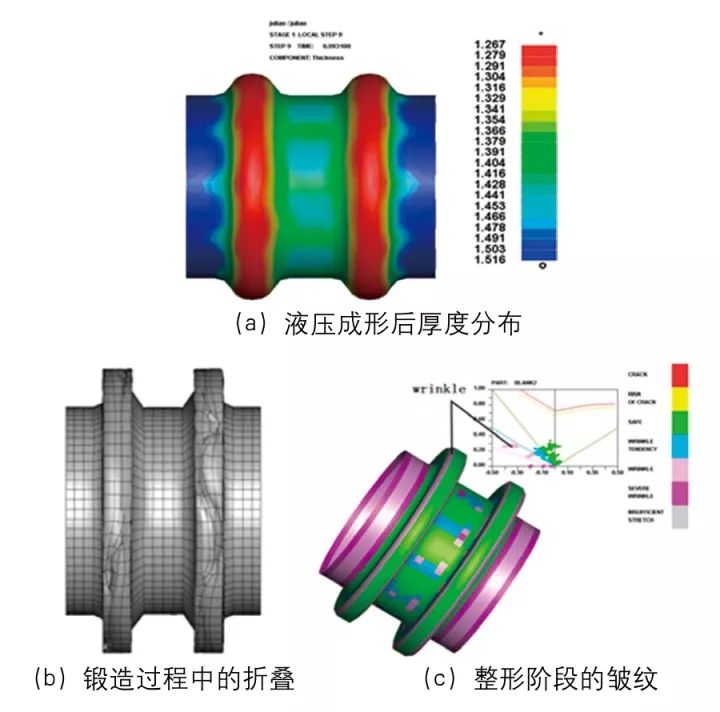
图7 载荷路径2下的模拟结果
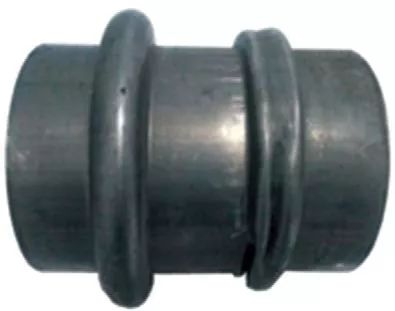
图8 应用载荷路径2所做实验中的折叠
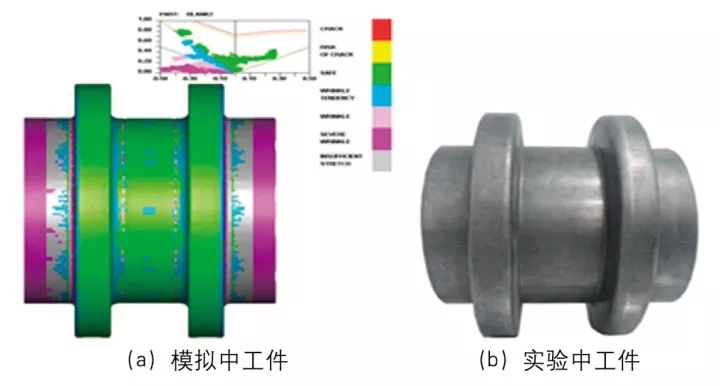
图9 采用载荷路径3液压胀形的工件
结束语
本文提出一种适用于空心薄壁构件的液压锻造新技术并开展了示范性应用。与传统的液压成形工艺相比,液压锻造工艺可以显著提高薄壁构件的成形性,有效解决具有大变形量和小圆角结构特征的制造加工。模拟和实验的分析结果表明,过度减薄容易发生在低压预胀形阶段,而褶皱和破裂易出现在后续的中压锻造阶段,内压加载路径的控制是液压锻造工艺的关键。通过工艺参数的优化,最终能够获得优异的成形效果。因此,空心薄壁构件液压锻造技术未来在汽车、航空航天等关键制造领域具有良好的应用前景和价值。